Role Of Defoamers/Antifoaming Agents In Textile Wet-Processing
Posted by barkha on March 17th, 2021
Foam is a colloidal structure of scattered or suspended gasses as fine bubbles in general. i.e. basically a bubble aggregate. More specifically, it is a liquid dispersion of steam, which forms the continuous phase of liquid. The phenomenon of foaming mostly depends on the properties of the interfaces and foaming is often coupled with an increase in the interface and hence the overall free energy of the device. Foam is essentially unstable and therefore self-destroying and its stability are determined, among other things, by the free interfacial energy gas/liquid, thus, textile defoamer chemical manufacturer produces these defoamers.
Challenges
The challenges associated with foaming in garment manufacturing industries must be known before we learn how to remove the foam with textile defoamer chemical. Differences in surfactant-based additives and air in wet textile processing can cause harmful effects due to the vigorous circulation of liquor.
Problems caused by moisture foam in textiles:
● Dense foam leads to severe tissue interlocking, caused by machinery stopping, uneven uptake and patchy dyeing.
● The spraying of the dye liquor will cause the material to float, resulting in unequal application of dye, in the dyed hanks and knitted fabrics.
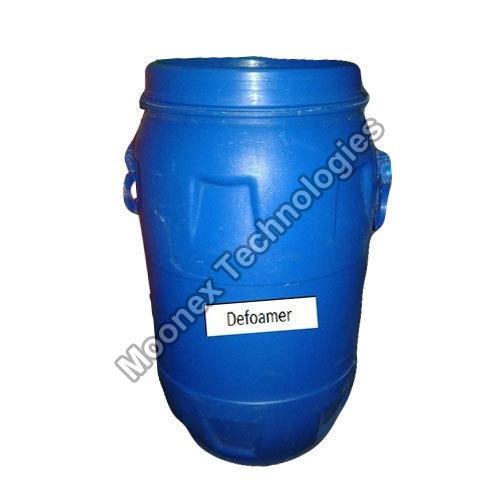
● The foam in the printing pad will cause a \'fish eye\' spot on printing tissue, in particular on rotary screen and roller printing.
The management of foaming by the careful optimisation of process parameters and the use of defoamers/anti-foamers etc is essential to remove the above problems.
Two related words are, technically speaking, spraying agents and spraying. The term defoamer is used to describe a product added to destroy existing moulds, whereas an anti-spray agent is a product added to a system to prevent the occurrence of foam. It is generally avoided to distinguish between the two terms as every spray agent has anti-spray properties and every anti-spray agent has certain de-sprays.
Mechanism Of Defoamers:
The defoamer\'s surface-active nature allows it to disperse very fast over every air-water interface. This is especially true if the interface is already covered by surfactants which tend to stabilize foams. This is the case. Hydrophobic Silica particles have the purpose of piercing and coalescing the surfaces of foam bubbles as the spreader stretches out at the interface. Differences in the relative value of these considerations can be expected depending on the specific anti-foam and foaming system:
● Antifoam dispersion in the solution of spraying
● Transportation of bulk droplets to the bubble interface
● Droplet in the interface of gas and liquid
● Extension
● Rupture of the Bubble
The surface-active stabilizer of the film stabilizes much of the foam. A potent surfactant spreads quickly on the broad surface of the film and displaces surfactants that are useful in light foams to reinforce the foam. In dense foams, the thicker aqueous is needed to penetrate the defoaming agent further.
Final Words
The weaknesses of activated polydimethylsiloxane contribute to the need for high-effectiveness, stable shear emulsions, durable pH, electrolyte and temperature tolerance. This results from the silicone fluid mechanical adjustment and improved emulsifying techniques. One such substance is Antifoam MX, which is available as an emulsion ready for use. Antiphoam MX is an example of an anti-foam that is highly efficient and engineered to allow low-foam structures in very limited doses.
There is therefore a wide range of textile processor anti-foams available, and an appropriate anti-foam must be identified according to the type of circumstance.